PRECISION TURNED PARTS AT HERBRIG & CO.
60 YEARS OF EXPERTISE – WHO WE ARE
Dreherei Herbrig & Co. GmbH stands for more than 60 years of precision mechanics in the best Saxon tradition. As a medium-sized family business from the Müglitz Valley, we are part of a historically grown business location that is known far beyond the local borders for its precision industry. The name Herbrig stands for high quality standards in precision turned parts. 200 employees and over 170 CNC sliding headstock lathes, CNC short lathes and rotary transfer machines ensure that well over 170 million CNC turned parts find their way to our customers every year.
DEVELOPMENT OF THE COMPANY
WHY MANUFACTURE WITH HERBRIG
MÜGLITZTAL LOCATION
Just a few kilometres away from the watchmaking town of Glashütte, Herbrig & Co. GmbH today represents the best tradition of Saxon precision mechanics.
The Müglitz Valley economic area is a valley landscape along the Müglitz stream in the Ore Mountains, with the internationally renowned watchmaking town of Glashütte/Saxony at its center. The Müglitz Valley is located in the district of Saxon Switzerland – Eastern Ore Mountains and stretches from the upper Ore Mountains (Geising) to the mouth of the Elbe (Heidenau).
Similar to regions such as the so-called Leuna-Wolfen-Bitterfeld chemical triangle or the concentration of furniture manufacturers in the Paderborn area, companies in the precision industry are concentrated in the Müglitz Valley. It is clear that the people of the regions are the decisive factor in the establishment of companies in similar sectors. The “precision knowledge” of the skilled workers is a major asset in the region.
History
After the start of mining around 1490 and the superficial extraction of ore, Saxony and the Müglitz Valley achieved relative prosperity. However, the rapid depletion of ore deposits, the Thirty Years’ and Seven Years’ Wars and the outbreak of the plague impoverished the region. The brief recovery through the reopening of previously unprofitable mines thanks to advances in mechanization, drive and mining technology was short-lived. In 1843, the Royal Saxon State Government decided to promote the establishment of industries in the impoverished region. The watchmaker Ferdinand Adolf Lange founded a watch company in 1845. Julius Assmann followed in 1850 and Moritz Großmann in 1854 with the establishment of their own watch manufactories.
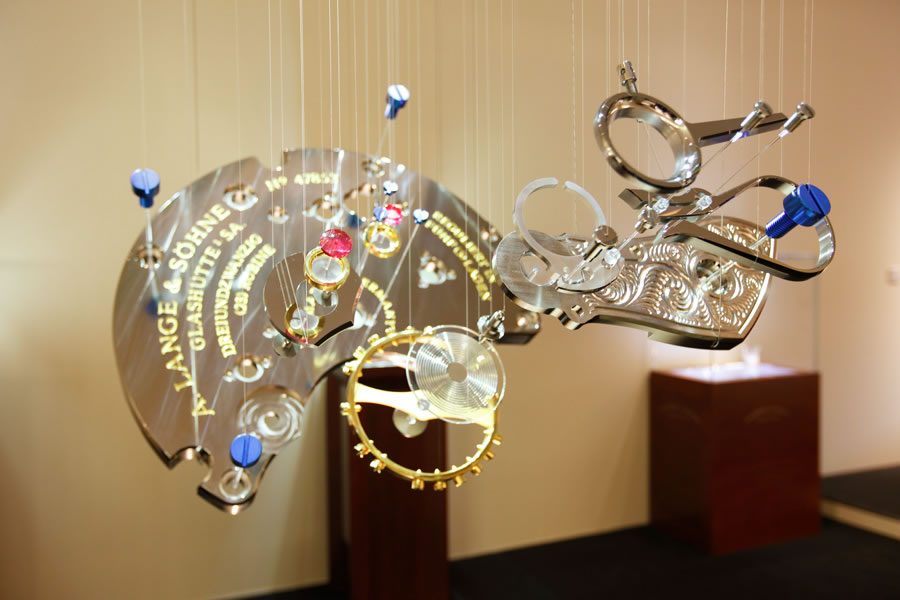